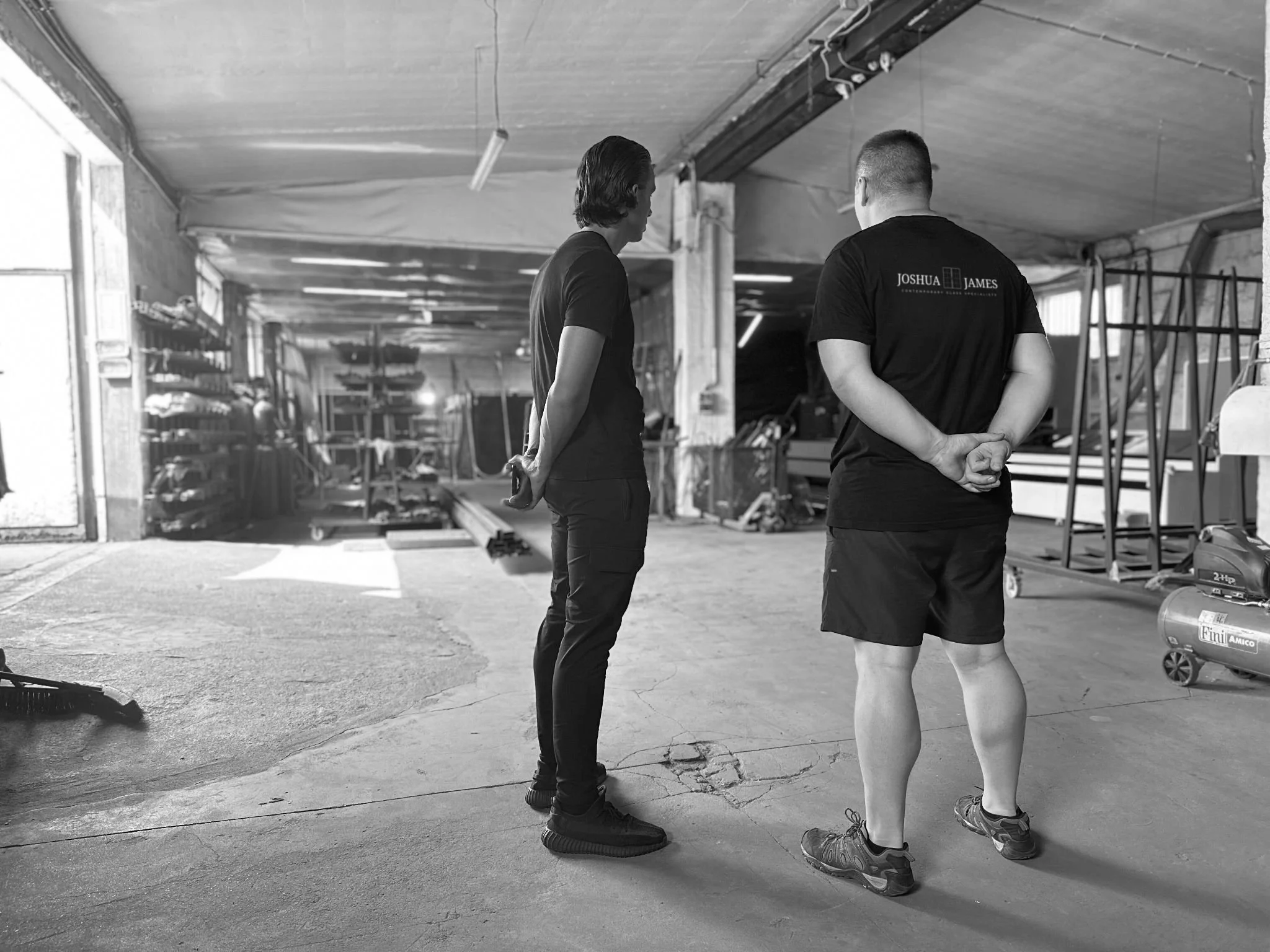
CRAFTING PERFECTION.
Discover the Artistry In Every Door Set.
Step1 | Design.
Every project begins with an idea, a vision from the client of exactly what they are looking to create. Whether a client knows exactly what they are looking for or requires some design inspiration our team are here to help.
Our fabrication process begins with a design. The team at Joshua James Ltd. works closely with the client, their architect or their chosen interior design team if appointed. They will guide the client through every design possibility, including door configurations, Cross Bar designs, handle options, choice of finishes and many more.
Once the design choices have been made by the client, they will then receive detailed drawings of every element of their project. Joshua James Ltd. offers unlimited design revisions to ensure that every client is 100% happy with their project before fabrication commences.

Designed In Days, Fabricated In Weeks, Admired For Decades.
Step 2 | Cutting.
Once the design for a project has been approved, the details are then passed over to the Joshua James Ltd. fabrication team where it begins its journey over the next few weeks. The fabrication process begins with each steel section required for the project being cut out using CNC technology to ensure laser precision and accuracy, leaving a clean finish to the edge of each profile. This allows every intricate detail on the project to be made to the millimetre.
Raw Sections Inspected & Buffed.
Once precision cut, each section is labeled, inspected and then buffered. Joshua James Ltd. takes pride in offering a smooth service to its clients, not only by offering incomparable customer service but also by ensuring each door is perfect. The buffering and inspection process ensures that each and every component used to craft our InoCross20 doors is perfect and passes the company’s quality control before welding begins.
Welding.
It is during the welding process that each project starts to really take shape. Each section is seamlessly welded, to form a Once the design for a project has been approved, the project is then passed over to the Joshua James Ltd. fabrication team where it begins its journey over the next few weeks. The fabrication process begins with each steel section required for the project being cut out using CNC technology to ensure laser precision and accuracy, leaving a clean finish to the edge of each profile. This allows every intricate detail on the project to be made to the millimetre.
Craftsmanship and attention to detail are two of many points that separate Joshua James Ltd. from the majority. Our fabrication team has deeply rooted experience, stemming back through generations. The team is the backbone of the family
Once the design for a project has been approved, the project is then passed over to the Joshua James Ltd. fabrication team where it begins its journey over the next few weeks. The fabrication process begins with each steel section required for the project being cut out using CNC technology to ensure laser precision and accuracy, leaving a clean finish to the edge of each profile. This allows every intricate detail on the project to be made to the millimetre.
Once the design for a project has been approved, the project is then passed over to the Joshua James Ltd. fabrication team where it begins its journey over the next few weeks. The fabrication process begins with each steel section required for the project being cut out using CNC technology to ensure laser precision and accuracy, leaving a clean finish to the edge of each profile. This allows every intricate detail on the project to be made to the millimetre.
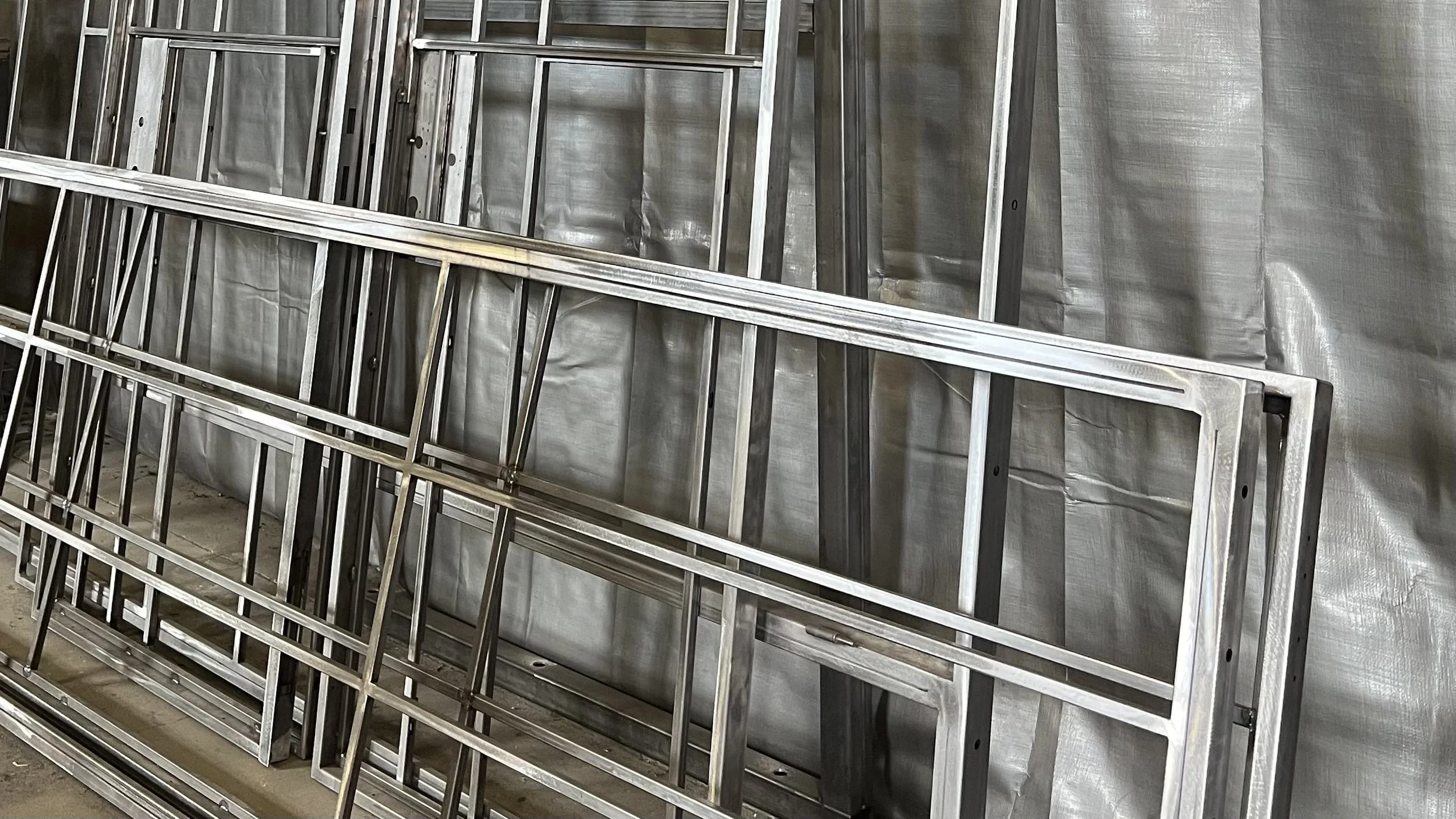